Random cuts
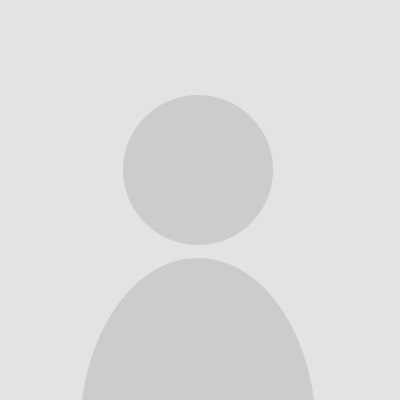
Quote from Richard Raven on February 3, 2021, 12:34 amHi,
2 weeks ago i received my Mini Gerbil. After install
i have been buzy to get it working with lightburn.At this time all engravings are working fine but when i try
to use the Fill and line option it goes wrong. The engraving
is oke but the lines are on top each other. It looks like the
X axle does not move. If i try to cut a panel it look like the
machine is cuttin at random.Homing and endstops are oke and working.
Can someone point me in the right direction
to solve this problem.Greeting Richard
Hi,
2 weeks ago i received my Mini Gerbil. After install
i have been buzy to get it working with lightburn.
At this time all engravings are working fine but when i try
to use the Fill and line option it goes wrong. The engraving
is oke but the lines are on top each other. It looks like the
X axle does not move. If i try to cut a panel it look like the
machine is cuttin at random.
Homing and endstops are oke and working.
Can someone point me in the right direction
to solve this problem.
Greeting Richard
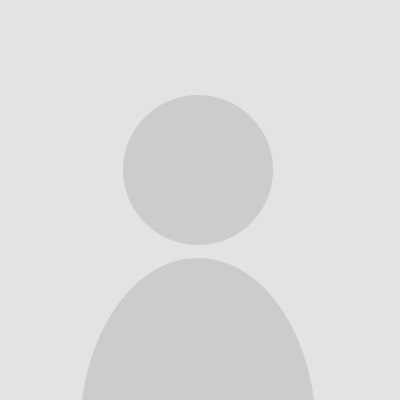
Quote from Paul on February 3, 2021, 9:42 amHave you tried to increase the little pot setting on the axis that does not move any more?
Try slower engraving speed and lower resolution e.g. 90 and see if that makes a difference. These actions might give you and us a clue where the issue lies. Also ensure that the belt is set correctly. Overtight belts can cause such issue.
Which laser program do you use?
Cheers, Paul
Have you tried to increase the little pot setting on the axis that does not move any more?
Try slower engraving speed and lower resolution e.g. 90 and see if that makes a difference. These actions might give you and us a clue where the issue lies. Also ensure that the belt is set correctly. Overtight belts can cause such issue.
Which laser program do you use?
Cheers, Paul
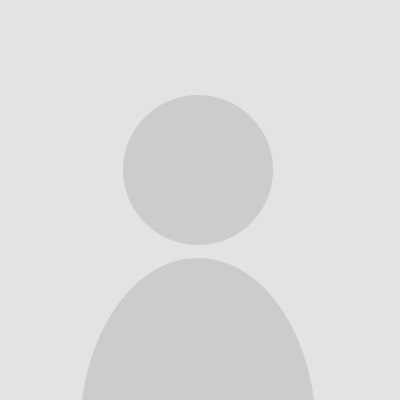
Quote from dancolwp1974 on February 3, 2021, 9:18 pmHi Richard,
the fact that homing and engraving is working fine is a great start, I'm struggling to think of a way that Mini Gerbil can get these right and yet get Fill+line wrong.
So I'm wondering if it's something about the Lightburn interface that is confusing or an inappropriate setting. If you're a new Lightburn user, please take a look at the Lightburn forum, and/or videos like https://www.youtube.com/watch?v=eeP3tneK-RI
Can anyone else point Richard in a helpful direction?
Thanks
DanPS A video would be helpful to show people what settings you're using and the response you see
Hi Richard,
the fact that homing and engraving is working fine is a great start, I'm struggling to think of a way that Mini Gerbil can get these right and yet get Fill+line wrong.
So I'm wondering if it's something about the Lightburn interface that is confusing or an inappropriate setting. If you're a new Lightburn user, please take a look at the Lightburn forum, and/or videos like https://www.youtube.com/watch?v=eeP3tneK-RI
Can anyone else point Richard in a helpful direction?
Thanks
Dan
PS A video would be helpful to show people what settings you're using and the response you see
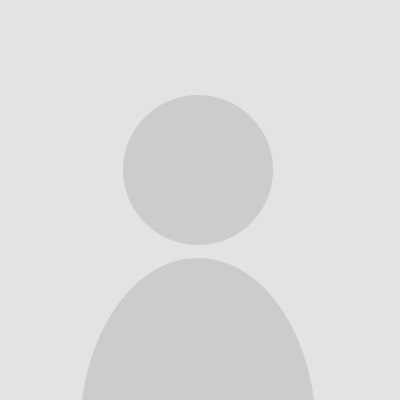
Quote from Richard Raven on February 5, 2021, 4:31 amThanks for the quick reaction.
i adjusted the stepper drivers (DRV8825 0.6V) and the belts, still got the same problem i added picture of the problem and also the settings, At this time i am using Lightburn v9.09 in the default settings , 0,0 upper left I think there is a problem with the coordiates. I have followed the exact installation instuctions from lightburn and Gerbil.
Grt Richard
Thanks for the quick reaction.
i adjusted the stepper drivers (DRV8825 0.6V) and the belts, still got the same problem i added picture of the problem and also the settings, At this time i am using Lightburn v9.09 in the default settings , 0,0 upper left I think there is a problem with the coordiates. I have followed the exact installation instuctions from lightburn and Gerbil.
Grt Richard
Uploaded files: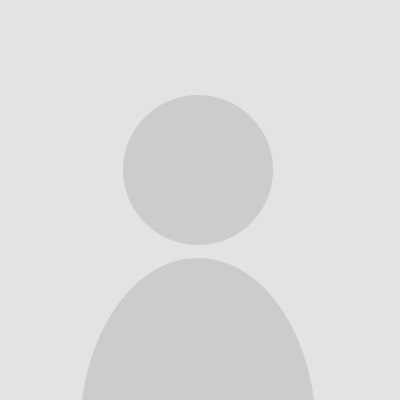
Quote from dancolwp1974 on February 6, 2021, 12:36 pmThanks Richard,
Fortunately there's a debugging step that splits the problem in half: the ability to save gcode files from Lightburn. The idea is that if you save the gcode file, we can examine the gcode file and see whether it makes sense. If it makes sense, it points to an issue downstream (ie. the controller). If it doesn't make sense, well then it's something with Lightburn.
Given I may end up eyeballing the gcode, I'd appreciate if you can find the simplest possible example of the problem you can, eg. start with a simple rectangle (drawn from the left hand side menu) and set it to line and fill. Test to see if it's a problem, and, once you've tweaked it to generate a problem, you can save the gcode file and email me.
Here's a screen image showing the 'Save gcode' button.
Thanks Richard,
Fortunately there's a debugging step that splits the problem in half: the ability to save gcode files from Lightburn. The idea is that if you save the gcode file, we can examine the gcode file and see whether it makes sense. If it makes sense, it points to an issue downstream (ie. the controller). If it doesn't make sense, well then it's something with Lightburn.
Given I may end up eyeballing the gcode, I'd appreciate if you can find the simplest possible example of the problem you can, eg. start with a simple rectangle (drawn from the left hand side menu) and set it to line and fill. Test to see if it's a problem, and, once you've tweaked it to generate a problem, you can save the gcode file and email me.
Here's a screen image showing the 'Save gcode' button.
Uploaded files: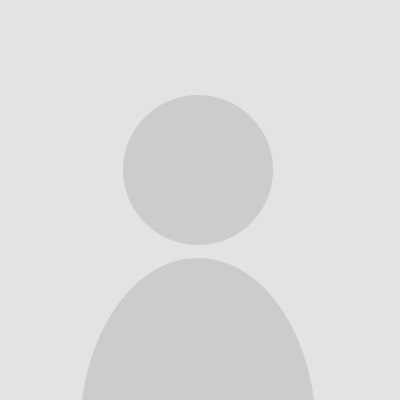
Quote from dancolwp1974 on February 7, 2021, 3:32 pmHi Richard,
could you try setting $21=0 please?
If that still doesn't work, I notice you've increased various speeds from their defaults quite substantially. The most likely reason for what you see is that you've exceeded the speeds that are physically possible for your machine.
What's physically possible for a given machine is dependent on the k40 axes weight (plus any custom add-ons that you've made), belt tension, alignment, friction, build quality and so forth.
When you increase the speed and acceleration settings as you have done, you allow the controller to send signals to the stepper motors faster than they can physically drive or accelerate the mechanical system. So the result you get is pretty much what you see - Lightburn sends a command to the laser and assumes the mechanical system has done as instructed. Meanwhile, the mechanical system hasn't physically moved as far as it was meant to before the next command comes along. Note that (unless you spend many thousands of dollars for a servo system), CNC (apart from the homing step) is an open loop system and thus the above is a not caused by a controller fault or limitation. So this is all resulting in 'a problem with coordinates' in that the system loses the knowledge of the laser head location.
For example, I note that you've increased your Y axis top speed to equal the X axis top speed. From a mechanical point of view, this doesn't make sense as the X axis just has to move a laser head, whereas the Y axis has to move the whole X axis (which includes the laser head). So Y axis has more mass and can't achieve the same performance dynamics.
We've set the default $ settings to reliably work on the vast majority of K40 units. Once you increase the settings, it comes down to your physical machine! Yes, you may be able to move quite a bit quicker than the default $ settings, but you may have to work for it by tuning belt tension, and all the mechanical hot-rodding aspects.
From here:
1 please reduce all your $ settings speeds and accelerations back to default (see https://awesome.tech/what-are-settings/).
2 Retest
3 If it works as desired, then my hypothesis above is verified. Your next steps are to focus on mechanical limitations, and at some point, accept that the design and build quality of the K40 is a limiting factor.
4 If you still get the same problems with standard $ settings, please advise and I can deep-dive into the gcode file you've provided.You may have had your high speeds work ok for other cut types (line, vs line and fill). This doesn't mean my hypothesis is incorrect, it just means that there really is a difference between what is required for line vs line and fill. For example, cutting an outline needs the laser to move more slowly to burn through the shape, whereas a fill engraving can move quickly as it doesn't need to dump as much energy onto the material to engrave. So trying to do two different activities in one action may be the problem, and you'll need to experiment to work out different sequences to see what's possible.
Regards,
Dan
Hi Richard,
could you try setting $21=0 please?
If that still doesn't work, I notice you've increased various speeds from their defaults quite substantially. The most likely reason for what you see is that you've exceeded the speeds that are physically possible for your machine.
What's physically possible for a given machine is dependent on the k40 axes weight (plus any custom add-ons that you've made), belt tension, alignment, friction, build quality and so forth.
When you increase the speed and acceleration settings as you have done, you allow the controller to send signals to the stepper motors faster than they can physically drive or accelerate the mechanical system. So the result you get is pretty much what you see - Lightburn sends a command to the laser and assumes the mechanical system has done as instructed. Meanwhile, the mechanical system hasn't physically moved as far as it was meant to before the next command comes along. Note that (unless you spend many thousands of dollars for a servo system), CNC (apart from the homing step) is an open loop system and thus the above is a not caused by a controller fault or limitation. So this is all resulting in 'a problem with coordinates' in that the system loses the knowledge of the laser head location.
For example, I note that you've increased your Y axis top speed to equal the X axis top speed. From a mechanical point of view, this doesn't make sense as the X axis just has to move a laser head, whereas the Y axis has to move the whole X axis (which includes the laser head). So Y axis has more mass and can't achieve the same performance dynamics.
We've set the default $ settings to reliably work on the vast majority of K40 units. Once you increase the settings, it comes down to your physical machine! Yes, you may be able to move quite a bit quicker than the default $ settings, but you may have to work for it by tuning belt tension, and all the mechanical hot-rodding aspects.
From here:
1 please reduce all your $ settings speeds and accelerations back to default (see https://awesome.tech/what-are-settings/).
2 Retest
3 If it works as desired, then my hypothesis above is verified. Your next steps are to focus on mechanical limitations, and at some point, accept that the design and build quality of the K40 is a limiting factor.
4 If you still get the same problems with standard $ settings, please advise and I can deep-dive into the gcode file you've provided.
You may have had your high speeds work ok for other cut types (line, vs line and fill). This doesn't mean my hypothesis is incorrect, it just means that there really is a difference between what is required for line vs line and fill. For example, cutting an outline needs the laser to move more slowly to burn through the shape, whereas a fill engraving can move quickly as it doesn't need to dump as much energy onto the material to engrave. So trying to do two different activities in one action may be the problem, and you'll need to experiment to work out different sequences to see what's possible.
Regards,
Dan