Wiring a 3-way switch
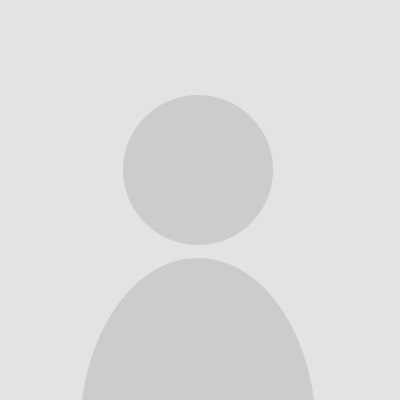
Quote from KranjskaKlobasa on June 30, 2019, 2:47 amA couple of months ago, Paul has already sent me the wiring diagram for wiring a 3-way switch in my K40, so there will be the option of also using the test button for mirror alignment.
I bought a 3-way switch with three terminals. The two outer terminals are S1 and S2 respectively, but I don't know, to which GND I must connect the middle GND switch terminal?
Must I connect it to the GND of the k40 power supply?
Thank you.
Regards.
A couple of months ago, Paul has already sent me the wiring diagram for wiring a 3-way switch in my K40, so there will be the option of also using the test button for mirror alignment.
I bought a 3-way switch with three terminals. The two outer terminals are S1 and S2 respectively, but I don't know, to which GND I must connect the middle GND switch terminal?
Must I connect it to the GND of the k40 power supply?
Thank you.
Regards.
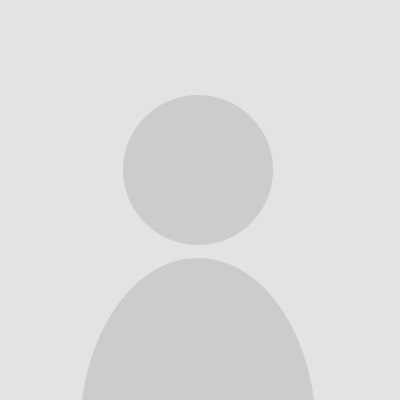
Quote from Paul on June 30, 2019, 8:40 amHi, the common (C) on the switch goes to the IN of the laser Power supply. S1 connects to the Mini Gerbil's PWM output and S2 connects to the middle lead of the potmeter.
However Dan found an easier way via software.
A simpler way to align and test fire the laser is to create a macro(s) in LightBurn (right click on the macro button).
And configure the macro as following:
$32=0
S200
M4
G4 P1000
M5
$32=1
What this does is, it sets the laser in CNC mode via $32 so it can fire the laser in stationary position. Than we set the laset strength to say 200 via the S parm. Fire the laser via M4 or M3. Dwell for 1000ms (G4). Switch off the laser and set the controller back to Laser mode.
Cheers, Paul
Hi, the common (C) on the switch goes to the IN of the laser Power supply. S1 connects to the Mini Gerbil's PWM output and S2 connects to the middle lead of the potmeter.
However Dan found an easier way via software.
A simpler way to align and test fire the laser is to create a macro(s) in LightBurn (right click on the macro button).
And configure the macro as following:
$32=0
S200
M4
G4 P1000
M5
$32=1
What this does is, it sets the laser in CNC mode via $32 so it can fire the laser in stationary position. Than we set the laset strength to say 200 via the S parm. Fire the laser via M4 or M3. Dwell for 1000ms (G4). Switch off the laser and set the controller back to Laser mode.
Cheers, Paul
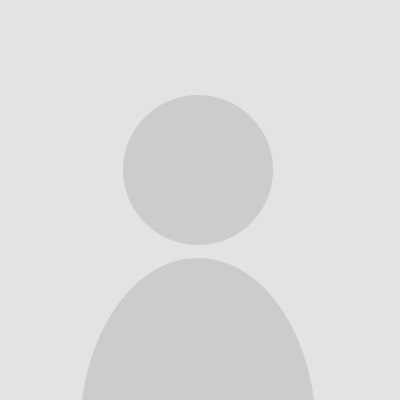
Quote from bront32 on October 4, 2019, 2:32 pmIf the PWM input to the LPS is internally filtered to an analogue voltage, then you could leave the pot in place and use a high speed semiconductor switch that is normally ON, to switch the pot wiper on and off from the mini-gerbil PWM output.
That way the Max Vin would be the pot wiper voltage and the PWM would be modulating that voltage to give a range from 0 to Vpot_wiper.
Just an idea to satisfy all those who want to keep the pot as a hardware current limit.
If the PWM input to the LPS is internally filtered to an analogue voltage, then you could leave the pot in place and use a high speed semiconductor switch that is normally ON, to switch the pot wiper on and off from the mini-gerbil PWM output.
That way the Max Vin would be the pot wiper voltage and the PWM would be modulating that voltage to give a range from 0 to Vpot_wiper.
Just an idea to satisfy all those who want to keep the pot as a hardware current limit.